Concrete Repair Principles and Methods
The European Standards EN1504 ‘Products and Systems for the protection and repair of concrete structures – Definitions, requirements, quality control and evaluation of conformity’, became mandatory throughout the European Economic Union with effect from the 1st January 2009. This series of standards has therefore now replaced all national standards for concrete repair and protection throughout the EEC, including in the UK.
Selection of the most Appropriate Concrete Repair Principles and Methods
To meet the owners future requirements, the appropriate concrete repair principles must be selected, then the best concrete repair method of achieving each concrete repair principle must be decided. These should be:
- Appropriate to the type, cause and extent of the concrete damage or defects i.e. Principle 3 Concrete Restoration.
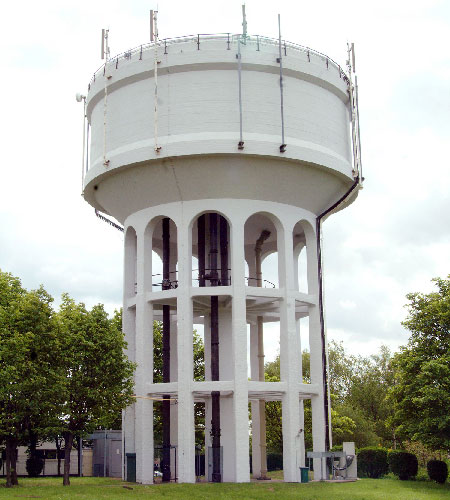
- Appropriate to the future requirements and the concrete repair Principles i.e. Method 3.1 Applying Concrete Repair Mortar by Hand or 3.2 Recasting the Concrete.
- Carried out with concrete repair products and systems that comply with the relevant Part of EN1504 i.e. Table 3 of EN 1504-3, item 7: Thermal compatibility, Part 1 Freeze-Thaw, etc.
The EN1504 Standards define 10 Principles for Concrete Repair and then Methods for achieving these Principles
Following assessment from the concrete condition survey and diagnosis of the concrete damage, together with the owners repair objectives and requirements, the appropriate concrete repair Principles can be selected.
This should be done in accordance with Part 9 of EN1504 which again divides the concrete repair Principles according to the root cause of the concrete damage, as follows:
Table 1 : Repair Principles and Methods Related to Defects in Concrete
Principle No | Principle and its Definition | Methods based on the Principle | Systems / Products |
---|---|---|---|
Principle 1 (P) |
Protection against Ingress. Reducing or preventing the ingress of adverse agents, eg water, other liquids, vapour, gas, chemicals and biological agents. |
1.1 Impregnation. Applying liquid products which penetrate the concrete and block the pore system. 1.2 Surface coating with and without crack bridging ability. 1.3 Locally bandaged/repaired cracks. 1.4 Filling cracks/voids. 1.5 Transferring cracks into joints. 1.6 Erecting external panels.1.7 Applying waterproof membranes. |
i.e. Hydrophobic impregnations. i.e. Impregnating coatings. i.e. protective coatings for chemical resistance, vapour permeability, crack bridging or colour etc., as required for the project. i.e. Repair Mortars and Resin Injection Systems, Sikadur Combiflex and Elastic Coatings. As Method 3 see above. i.e. Repair Mortars and Joint Sealants i.e. Panel Systems and Structural Glazing Silicones i.e. Sheet Membranes and Liquid Applied Membranes. |
Principle 2 (MC) |
Moisture Control. Adjusting and maintaining the moisture content in the concrete within a specified range of values. |
2.1 Hydrophobic impregnation. 2.2 Surface Coating. 2.3 Sheltering or over cladding. 2.4 Electrochemical treatment. |
i.e. Hydrophobic impregnations. As for Method 1.2 see above. i.e. Resin Coating and Flooring Systems and Liquid Applied Membranes. A process, no specific repair materials. |
Principle 3 (CR) |
Concrete Restoration. Restoring the original concrete of an element of the structure to the originally specified shape and function. Restoring the concrete structure by replacing part of it. |
3.1 Applying mortars by hand. 3.2 Recasting with concrete. 3.3 Spraying concrete or mortar. 3.4 Replacing elements. |
i.e. Pre-bagged Repair Mortars. i.e. Pourable mortars and grouting systems or special admixtures. i.e. Machine applied mortar systems. i.e. Epoxy and polymer improved adhesives. |
Principle 4 (SS) |
Structural Strengthening. Increasing or restoring the structural load bearing capacity of an element of the concrete structure. |
4.1 Adding or replacing embedded or external reinforcing steel bars. 4.2 Installing bonded steel rebars in preformed or drilled holes in the concrete. 4.3 Plate bonding. 4.4 Adding mortar or concrete. 4.5 Injecting cracks, voids or other interstices. 4.6 Filling cracks, voids or interstices. 4.7 Prestressing (post- tensioning). |
i.e. Sika CarboDur and SikaWrap ranges with Sikadur adhesive. i.e. Resin anchors and grout systems. i.e. Sika CarboDur range with Sikadur adhesive systems. i.e. Epoxy or polymer bonding bridges. i.e. Injection Resins. i.e. Injection Resins. i.e. Sika CarboStress systems. |
Principle 5 (PR) |
Physical Resistance. Increasing resistance to physical or mechanical attack. |
5.1 Overlays or coatings. 5.2 Impregnation. |
As for Method 1.2 see above. i.e. Resin floor systems. |
Principle 6 (RC) |
Resistance to Chemicals. Increasing resistance of the concrete surface to deteriorations by chemical attack. |
6.1 Overlays or coatings. 6.2 Impregnation. |
As for Method 1.2 see above. As for Method 5.2 see above. |
Table 2 : Concrete Repair Principles and Methods Related to Reinforcement Corrosion
Principle No | Principle and its Definition | Methods based on the Principle | Systems / Products |
---|---|---|---|
Principle 7 (RP) |
Preserving or Restoring Passivity. Creating chemical conditions in which the surface of the reinforcement is maintained in or is returned to a passive condition. |
7.1 Increasing cover to reinforcement with additional cementitious mortar or concrete. 7.2 Replacing contaminated or carbonated concrete. 7.3 Electrochemical realkalisation of carbonated concrete. 7.4 Realkalisation of carbonated concrete by diffusion. 7.5 Electrochemical chloride extraction. |
i.e. Repair mortar ranges. As for methods 3.2, 3.3, 3.4 see above. i.e. Sikagard 720 EpoCem for alkali resistant post treatment. As for Method 7.3 see above. As for Method 7.3 see above. |
Principle 8 (IR) |
Increasing Resistivity. Increasing the electrical resistivity of the concrete. |
8.1 Limiting moisture content by surface treatment, coatings or sheltering. | As for Method 1.1, 1.2 and 2.3 see above. |
Principle 9 (CC) |
Cathodic Control. Creating conditions in which potentially cathodic areas of reinforcement are unable to drive an anodic reaction. |
9.1 Limiting oxygen content (at the cathode) by saturation or surface coating. | i.e. Sika FerroGard 903 Corrosion Inhibiting Impregnation. |
Principle 10 (CP) | Cathodic Protection. | 10.1 Applying electrical potential. | i.e. Sika Galvashield systems. |
Principle 11 (CA) |
Control of Anodic areas. Creating conditions in which potentially anodic areas of reinforcement are unable to take part in the corrosion reaction. |
11.1 Painting reinforcement with coatings containing active pigments. 11.2 Painting reinforcement with barrier coatings. 11.3 Applying corrosion inhibitors to the concrete. |
i.e. Epoxy and cement slurry systems i.e. Epoxy and cement slurry systems. i.e. Sika FerroGard 903 corrosion inhibitor. |
Important Note: The EN 1504 Standards state that the absence of a specific concrete repair or concrete protection Method from this table does not mean that such a Method or system is necessarily unsatisfactory. Specific concrete repair Methods and materials, including new technologies and developments that are not yet widely proven and established, may still be used in appropriate circumstances and situations.
In response to requests from our customers we have also now added an Online Shop where the most commonly required EN 1504 Tested and Approved Concrete Repair and Concrete Façade Protection Products can be selected and ordered if you know what you require.
If you would like more specific guidance on the EN1504 Concrete Repair Principles and Methods in relation to your specific concrete repair project, please call any of our offices and one of our concrete repair experts will be happy to assist you.